In August 2019 the TU Vienna Spaceteam visited the company “Austin Powder” to carry out measures for the new upper stage ignition. The ignition of the upper stage during the flight is essential in order to carry out a successful of our two-staged concept for “The Hound”. However, due to the face that up to this point the upper stage ignitions did not work too reliably, we have been looking for alternative ways of igniting it.
Criteria
In order to pick a choice, the points below had to be considered:
- Logical aspect
- Availability in both, Austria and the US
- Legal handling
- Technical aspect
- Is the rate of burn off depending on the pressure?
- Is a nozzle-plug required?
- Which form/shape is the pyrogen being delivered? (powder, pellets)
- How is the pyrogen being attached in the motor?
- Is it possible to safely integrate the ignite into the rocket?
- How much mass of the pyrogen is required?
- Is there any interaction between the pyrogen and the O-ring? If yes, could it cause any leakages or a failure of the motor?
- Safety aspect
- Characteristics of the chemicals (causing irritations, acidly, easily inflammable,…)
- How is the handling of the chemicals?
Succesful Ignition
With the criteria below a successful ignition of a commercial motor should be possible. The values are empirical.
- Temperature of the flame >1000°C
- The flue gases should hold the motor at a pressure of more than 2 bars for a time of more than 200ms
- The pressure inside the motor must not exceed 30 bars during the ignition
Boron potassium nitrate (BKNO 3)
Amongst a huge amount of possibilities, our team decided in favor of boron potassium nitrate. The constituents amorphous boron and potassium nitrate are available for us in Austria, as well as in the US (1a). Since we require professional support for legal usage in Austria, the tests were executed at a location specifically for testing purposes of the company Austin Powder and under the supervision of members of their staff.
BKNO3 fulfills the first criterium for a successful ignition, both remaining criteria are being tested as well.
Setup used for the tests
For receiving meaningful results of the tests, the conditions under which the tests were performed were set up as realistically as possible. The geometric conditions are as follows. The volume of the motor is about the same as the setup pictured in image 1, the diameter of the nozzle of motor and test stand are identical.
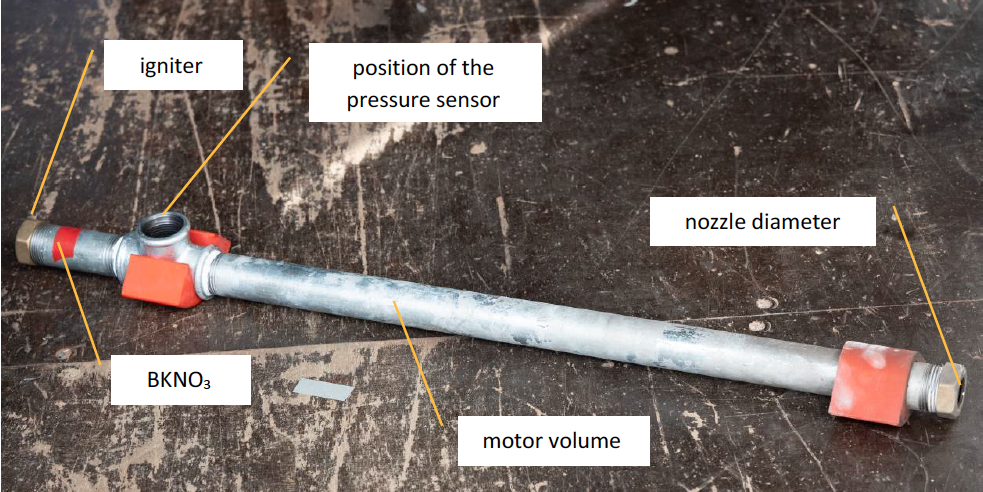
The second condition is the ambient pressure. The planned height at which “The Hound” ignites the second stage is at about 10 km. At that height, there is an ambient pressure of about 0.25 bars. To simulate these conditions it is required to lower the ambient pressure of the test setup in a vacuum chamber. The used chamber has a significantly bigger volume than the setup itself in order for the pressure inside to only increase slightly while the motor is burning (image 2).
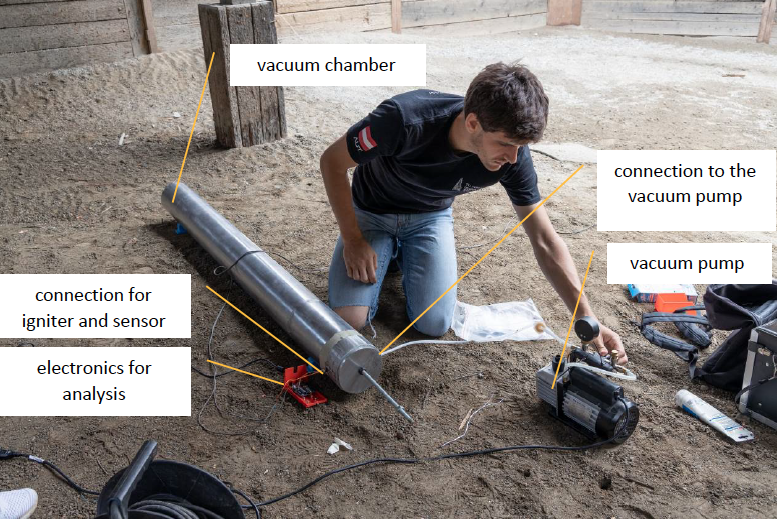
The pressure sensor is located with some distance to the BKNO3. The screws are sealed with teflon so the flue gases are only able to escape through the end of the pipe. The pressure sensor measures the pressure evolution over time in the test setup during burning time.
Execution of the test
For the first test 2g BKNO3 were used. The pressure was lowered to about 0.1 bar absolut pressure at all tests. That is less than the required maximum of 0.25 bar. Unfortunately the data record stopped before the ignition. However, the test showed that an ignition under the given circumstances is possible without any problems. After the test no burnt remainings of the BKNO3 could be found in the vacuum chamber.
After a restart of the program we increased the amount of BKNO3 to 4g, 6g and 8g.
After 8g the tests were stopped because the closure of the vacuum chamber opened. The gas that are released by the BKNO3 wouldn´t suffice to create an overpressure in the vacuum pressure.
The test setup wasn´t fixated axially. That´s why it can be presumed that the combustion’s impulse, caused by the BKNO3 pushed the lid open. As mentioned in chapter two the maximum pressure is supposed to stay below 30 bar. At the last test a maximum pressure of 23 bar was measured. It is to assume that an increase of the BKNO3 to 10g would have caused an exceedance of the maximum pressure. That´s why a decision against further tests, using 10g, was made.
Analysis
Shortly after the ignition the pressure rises immediately but breaks right afterwards. The second increase reaches a clearly lower maximum. However, the flue gases require some time until they have left the test setup through the nozzle.
At the last try with 8g is the measured pressure at the end higher than expected because the lid was pushed open and the sensor measures the ambient pressure.
All recorded curves show the same characteristics. Right after the ignition a sudden rise in pressure occurs and lasts around 15 ms. It is especially notable that that time stays about the same, the pressure however peaks at higher values when more BKNO3 is used (image 4). That is likely caused by a compression wave that hurries ahead. The pressure breaks down, almost to the original value, before it rises again a few milliseconds later.
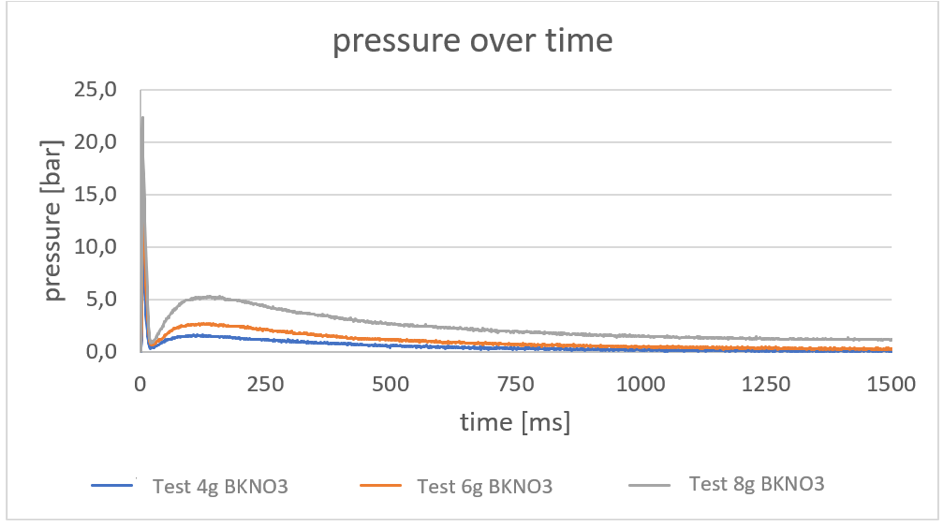
Summary
The tests have shown that BKNO3 can be ignited without any problems at low pressure and in order to satisfy all criteria from chapter 2 around 6-8g BKNO3 are needed (2f).
After the logical aspects, the remaining criteria are being talked about now. The tests have shown, that a low pressure doesn’t influence the burning significantly (2a), so nozzle plug isn’t needed (2b). The pyrogen can be fixed inside the motor using a basket which doesn’t have any negative impact on the O-rings (2d, 2e, 2g).
From the safety aspect BKNO3 is to handle the same way as black powder. BKNO3 is neither acidly nor irritating, however, easily inflammable (3a, 3b).
At this point we would like to thank Dr. Kappl (http://www.energeticmaterials.at/) and the company Austin Powder for their friendly support.