LAMARR
The TU Wien Space Team’s Bi-Liquid Rocket Project
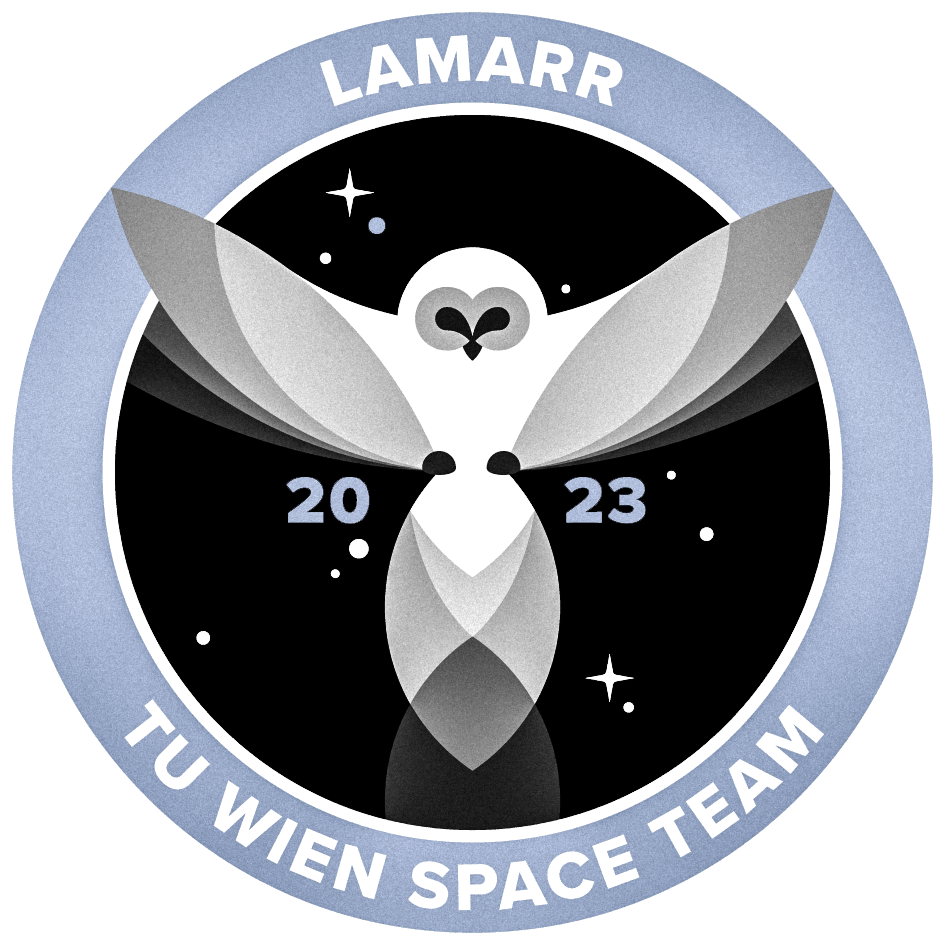
About the Project
Lamarr is the second liquid-propellant rocket developed by the TU Wien Space Team and a major milestone for student rocketry in Austria. Our goal is to build a rocket powered by ethanol and liquid oxygen (LOX) that can reach an altitude of 9 kilometers. The project combines cutting-edge technology, extensive testing, and interdisciplinary teamwork.
Mission & Objectives
With our rocket Hedy, we aim to:
- Successfully reach an altitude of 9 km
- Ensure a safe recovery using a two-stage parachute system
- Collect comprehensive telemetry data throughout the flight
- Document and pass on knowledge for future generations of students


Propulsion
Hedy is powered by a pressure-fed liquid bipropellant engine, developed entirely in-house. The rocket uses cryogenic liquid oxygen (LOX) as the oxidizer and ethanol as the fuel. This system allows precise control of the propellant flow and optimized combustion efficiency.

Aerostructure
We designed our rocket for stability and weight optimization. The GFRP nose cone is aerodynamically shaped, while the main body is made from CFRP to keep the weight as low as possible. We refined the design using intricate simulations to minimize drag.
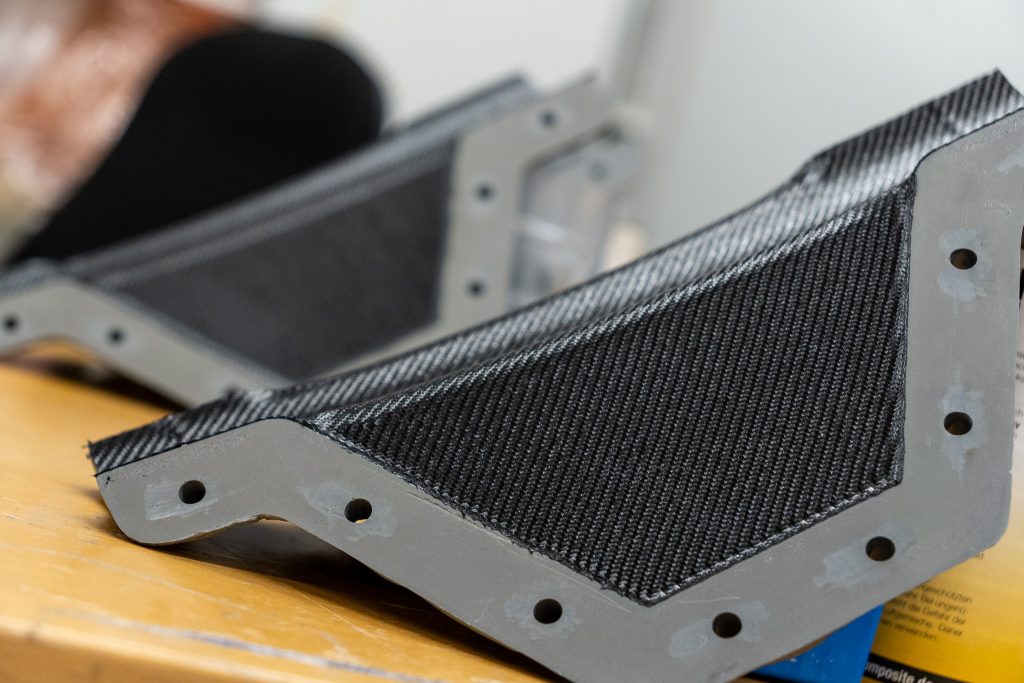
RECOVERY
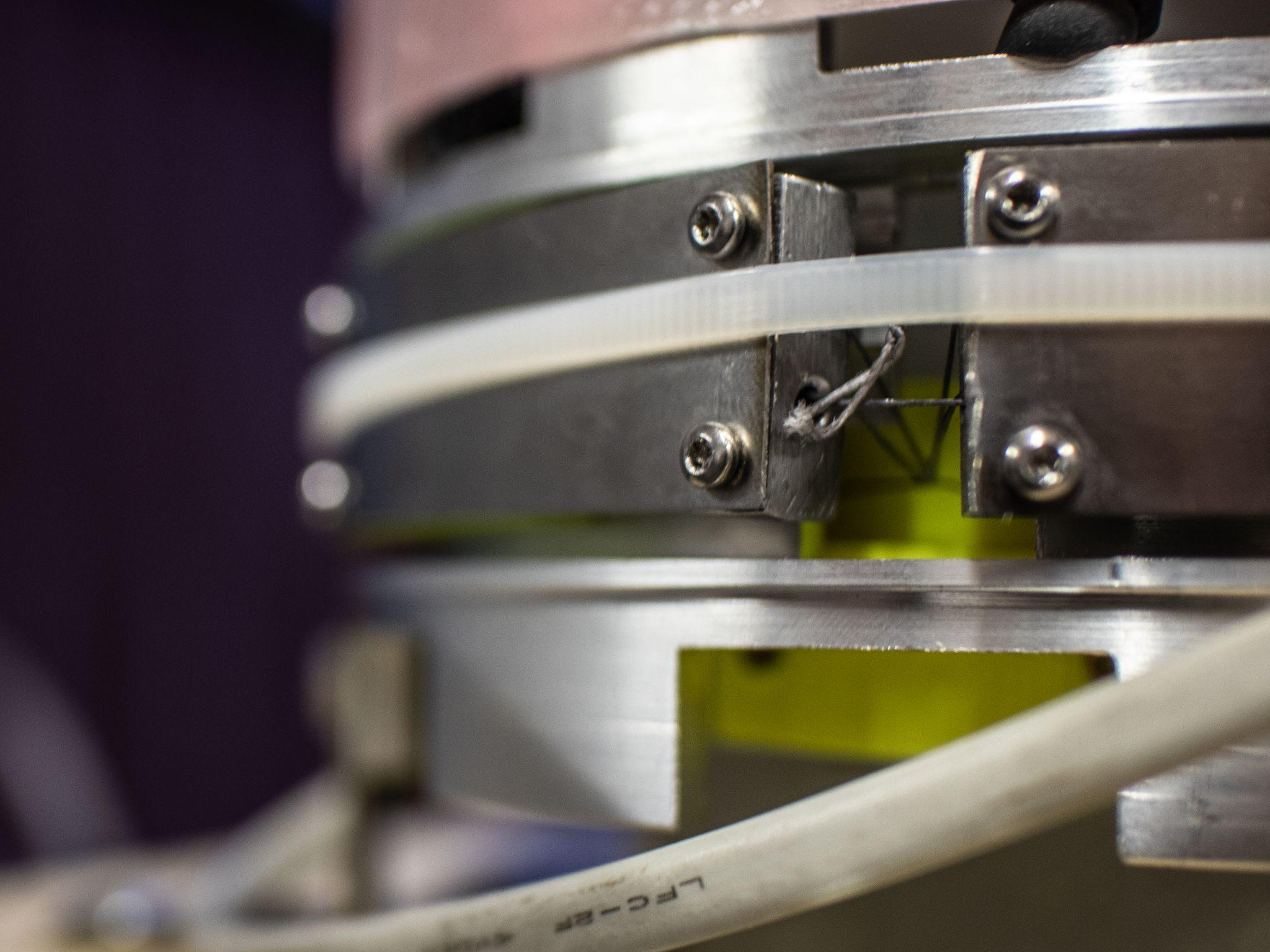
To ensure a safe descent and landing, Hedy features a two-stage parachute system. After reaching its peak altitude, a drogue chute deploys to slow the descent. Later, the main parachute opens to allow for a smooth landing. We extensively tested the system and it operates without pyrotechnics, improving reliability.
Avionics
All electronics, from flight control and data logging to telemetry transmission, we developed in-house. A custom-built ground station receives real-time data throughout the flight, including positional tracking and critical sensor readings from the propulsion system.
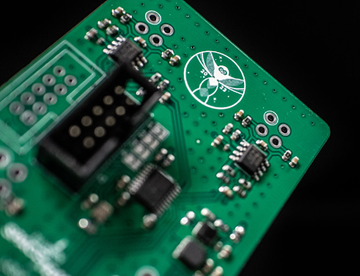
Ground Support Equipment
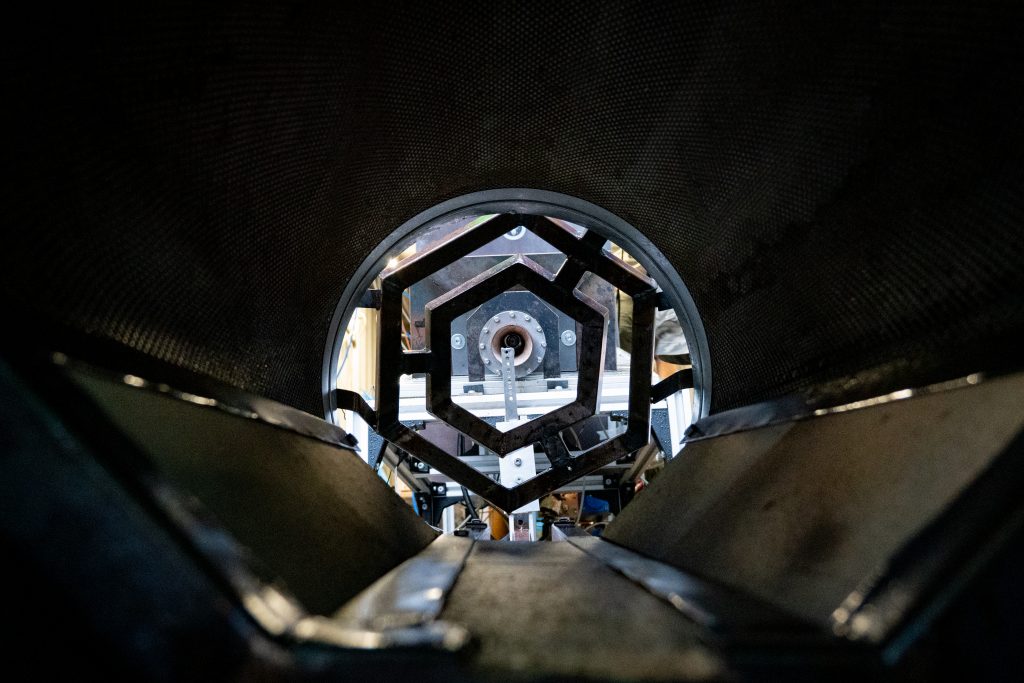
To ensure safe and controlled testing, we have developed a specialized ground support system. This infrastructure allows for remote fueling, monitoring, and operation of the rocket. Our next major milestone is a static fire test, where we ignite the engine of the flight ready rocket, without letting it lift off from the ground.
Why is Lamarr Special?
Lamarr is a liquid-propellant rocket project developed entirely by students in Austria. We are known for building the most light-weight bi-liquid rockets among student rocketry teams in Europe. The project bridges engineering, physics and computer science offering students a rare opportunity to gain hands-on experience in real-world rocketry, from concept development to full-scale testing.
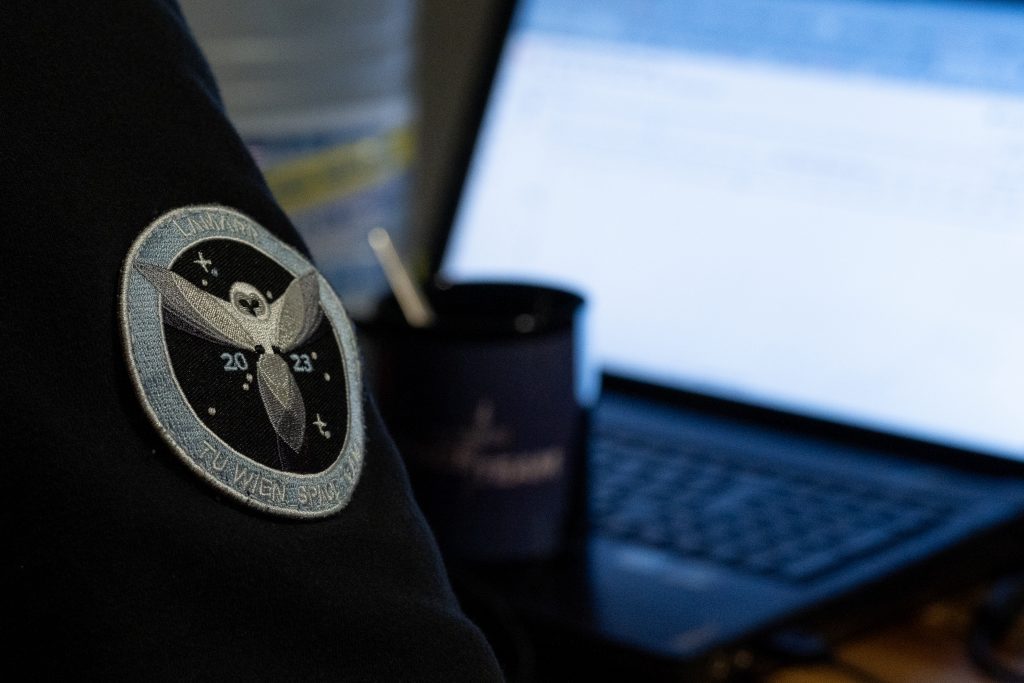
Join the Project!
We are always looking for passionate new members, whether you’re interested in propulsion systems, aerodynamics, electronics, software, or recovery systems. If you want to help develop cutting-edge space technology, reach out to us or visit our next Recruiting Event!
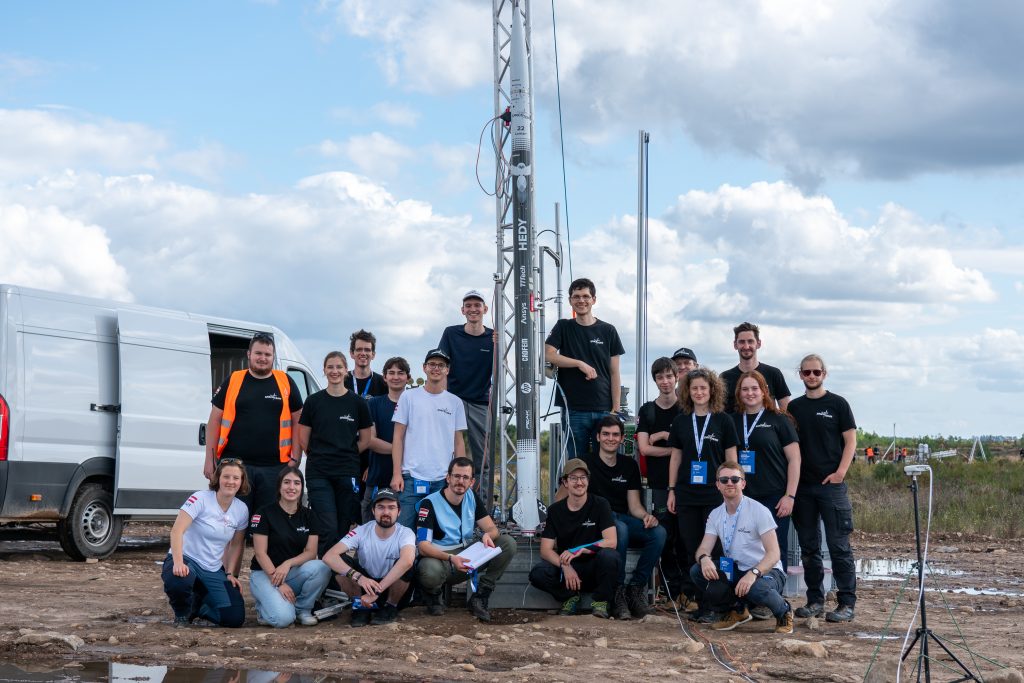